The field of chemical applications has witnessed significant advancements in recent years, driven by innovations in technology and manufacturing processes. One such innovation is the integration of Computer Numerical Control (CNC) machining, which has revolutionized the way chemical equipment and components are designed and produced. CNC machining has become an indispensable tool in the chemical industry, offering unparalleled precision, speed, and versatility. In this article, we will explore the five ways CNC machining enhances chemical applications.
Increased Precision and Accuracy
Image: 

One of the primary advantages of CNC machining in chemical applications is its ability to achieve unprecedented levels of precision and accuracy. Chemical equipment and components require exacting specifications to ensure optimal performance, safety, and compliance with regulations. CNC machining enables the production of complex geometries and precise features, which are crucial in chemical applications such as reactors, heat exchangers, and pipelines.
CNC machining utilizes computer-aided design (CAD) software and computer-aided manufacturing (CAM) software to create detailed designs and simulations. This allows for the creation of complex shapes and features that would be impossible to produce using traditional manufacturing methods. The precision and accuracy of CNC machining also reduce the risk of human error, ensuring that chemical equipment and components meet the required specifications.
Improved Material Selection and Compatibility
Image: 

CNC machining offers the flexibility to work with a wide range of materials, including metals, plastics, and ceramics. This is particularly important in chemical applications, where equipment and components must be compatible with various chemicals and operating conditions. CNC machining enables the selection of materials that are resistant to corrosion, erosion, and other forms of degradation, ensuring the longevity and reliability of chemical equipment and components.
The use of CNC machining also allows for the creation of complex material combinations and hybrid structures, which can enhance the performance and durability of chemical equipment and components. For example, CNC machining can be used to create composite materials with unique properties, such as high-temperature resistance or chemical resistance.
Enhanced Surface Finish and Quality
Image: 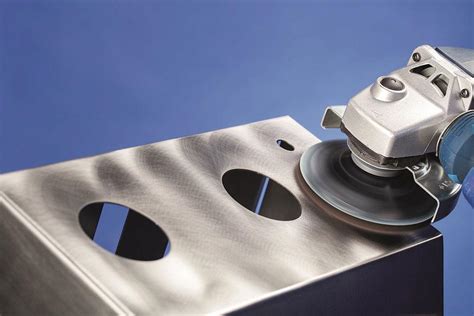
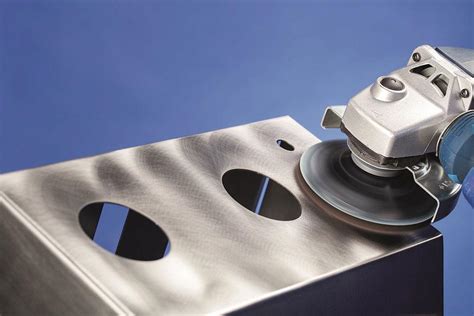
CNC machining is capable of producing surface finishes that are superior to those achieved through traditional manufacturing methods. The precision and control offered by CNC machining enable the creation of smooth, polished surfaces that are essential in chemical applications. A high-quality surface finish reduces the risk of corrosion, erosion, and other forms of degradation, ensuring the longevity and reliability of chemical equipment and components.
The use of CNC machining also allows for the creation of complex surface features and textures, which can enhance the performance and functionality of chemical equipment and components. For example, CNC machining can be used to create surface roughness or texture that improves the bonding strength of coatings or linings.
Increased Efficiency and Productivity
Image: 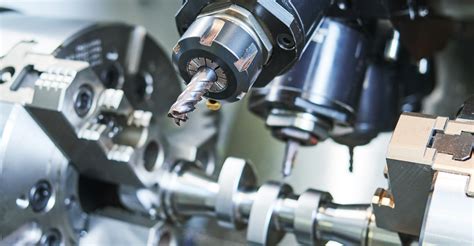
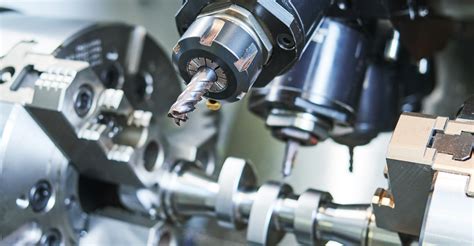
CNC machining offers significant advantages in terms of efficiency and productivity, particularly in high-volume production environments. The use of CNC machining enables the automation of manufacturing processes, reducing the risk of human error and increasing the speed of production. CNC machining also allows for the optimization of manufacturing processes, reducing waste and improving material utilization.
The integration of CNC machining with other technologies, such as robotics and automation, can further enhance efficiency and productivity in chemical applications. For example, CNC machining can be used to create complex components that are assembled using robotic systems, reducing the need for manual labor and improving overall efficiency.
Reduced Lead Times and Improved Responsiveness
Image: 

CNC machining offers significant advantages in terms of lead times and responsiveness, particularly in applications where rapid prototyping and production are critical. The use of CNC machining enables the rapid creation of complex components and prototypes, reducing the need for manual labor and improving overall efficiency.
The integration of CNC machining with other technologies, such as 3D printing and additive manufacturing, can further enhance responsiveness and reduce lead times in chemical applications. For example, CNC machining can be used to create complex components that are assembled using additive manufacturing techniques, reducing the need for manual labor and improving overall efficiency.
Gallery of CNC Machining in Chemical Applications:

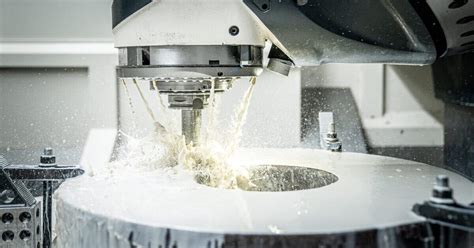
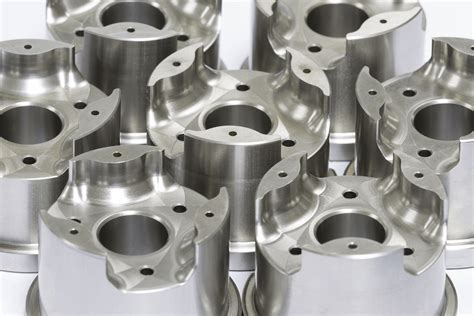

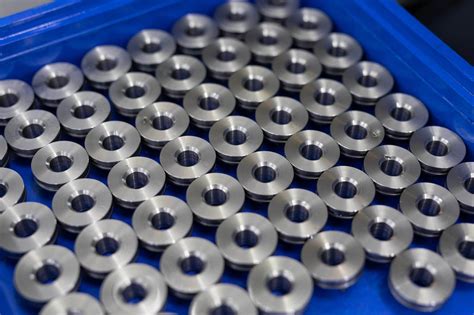
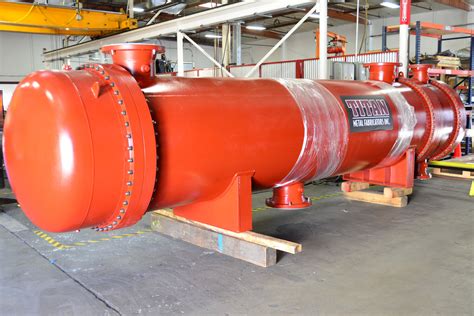
FAQs:
What is CNC machining, and how does it work?
+CNC machining is a manufacturing process that uses computer-controlled machines to create complex components and parts. The process involves the use of CAD software to design the component, which is then translated into a set of instructions that the CNC machine follows to create the part.
What are the advantages of CNC machining in chemical applications?
+CNC machining offers several advantages in chemical applications, including increased precision and accuracy, improved material selection and compatibility, enhanced surface finish and quality, increased efficiency and productivity, and reduced lead times and improved responsiveness.
What types of materials can be used in CNC machining for chemical applications?
+CNC machining can be used to work with a wide range of materials, including metals, plastics, and ceramics. The choice of material depends on the specific requirements of the application, including factors such as corrosion resistance, temperature resistance, and chemical compatibility.
In conclusion, CNC machining has revolutionized the field of chemical applications, offering unparalleled precision, speed, and versatility. The use of CNC machining enables the creation of complex components and parts with improved material selection and compatibility, enhanced surface finish and quality, and increased efficiency and productivity. As the chemical industry continues to evolve, the role of CNC machining is likely to become even more critical, enabling the development of innovative solutions to complex challenges.