In the world of labeling, accuracy and efficiency are key. Whether you're a business owner looking to boost your brand's visibility or a consumer seeking to organize your personal belongings, understanding the different label application methods can make all the difference. In this article, we'll delve into six label application methods you need to know, exploring their benefits, drawbacks, and ideal uses.
The Importance of Label Application
Before we dive into the various methods, it's essential to understand the significance of label application. Labels serve as a means of identification, providing crucial information about a product, package, or item. They can include details such as product names, prices, ingredients, instructions, and warnings. Effective label application ensures that labels are securely attached, easy to read, and visually appealing.
Method 1: Hand Application
Hand application involves attaching labels to products or packages manually. This method is often used for small-scale labeling operations or when a high level of precision is required.

Benefits:
- Allows for high precision and control
- Suitable for small-scale labeling operations
- No initial investment in machinery required
Drawbacks:
- Time-consuming and labor-intensive
- May lead to inconsistent label placement
Method 2: Machine Application
Machine application uses specialized equipment to attach labels to products or packages. This method is commonly used in high-volume labeling operations.

Benefits:
- Fast and efficient
- Consistent label placement
- Suitable for high-volume labeling operations
Drawbacks:
- Requires significant initial investment in machinery
- May require trained personnel to operate
Method 3: Semi-Automatic Application
Semi-automatic application combines manual and machine-based labeling. This method is ideal for businesses that require a moderate level of labeling precision and volume.

Benefits:
- Offers a balance between precision and efficiency
- Suitable for moderate-volume labeling operations
- Less expensive than fully automatic machinery
Drawbacks:
- May require manual adjustment and monitoring
- Limited to specific label sizes and shapes
Method 4: Thermal Transfer Labeling
Thermal transfer labeling uses heat to transfer images and text onto labels. This method is commonly used for creating high-quality, durable labels.
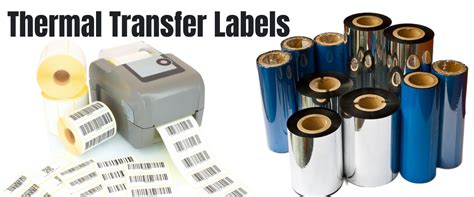
Benefits:
- Creates high-quality, durable labels
- Suitable for a wide range of materials and surfaces
- Can produce complex label designs
Drawbacks:
- Requires specialized equipment and supplies
- Can be expensive for small-scale labeling operations
Method 5: Inkjet Labeling
Inkjet labeling uses a printer to apply ink-based labels onto products or packages. This method is ideal for creating high-quality, variable data labels.

Benefits:
- Creates high-quality, variable data labels
- Suitable for a wide range of materials and surfaces
- Can produce complex label designs
Drawbacks:
- Requires specialized equipment and supplies
- Can be expensive for small-scale labeling operations
Method 6: Laser Labeling
Laser labeling uses a laser to etch or burn images and text onto labels. This method is commonly used for creating high-quality, durable labels with intricate designs.

Benefits:
- Creates high-quality, durable labels with intricate designs
- Suitable for a wide range of materials and surfaces
- Can produce complex label designs
Drawbacks:
- Requires specialized equipment and supplies
- Can be expensive for small-scale labeling operations
Choosing the Right Label Application Method
With so many label application methods available, choosing the right one for your business or personal needs can be overwhelming. Consider the following factors when selecting a method:
- Label volume and frequency
- Label size and shape
- Material and surface type
- Desired level of precision and control
- Budget and resources
Label Volume and Frequency
If you require high-volume labeling, machine application or semi-automatic application may be the best option. For small-scale labeling operations, hand application or thermal transfer labeling may be more suitable.
Label Size and Shape
Consider the size and shape of your labels when selecting a method. Some methods, such as machine application, may be limited to specific label sizes and shapes.
Material and Surface Type
Different label application methods are suitable for various materials and surfaces. For example, thermal transfer labeling is ideal for creating durable labels on metal or plastic surfaces.
Desired Level of Precision and Control
If you require a high level of precision and control, hand application or semi-automatic application may be the best option.
Budget and Resources
Consider your budget and resources when selecting a label application method. Some methods, such as machine application, may require significant initial investment in machinery and supplies.
Conclusion
In conclusion, the right label application method can make all the difference in your labeling operations. By understanding the benefits and drawbacks of each method, you can choose the best approach for your business or personal needs. Whether you're looking for precision, efficiency, or high-quality labels, there's a label application method that's right for you.
Gallery of Label Application Methods


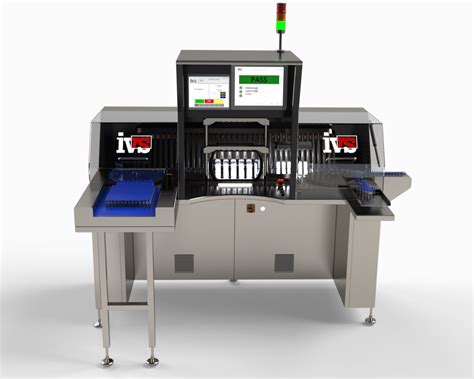

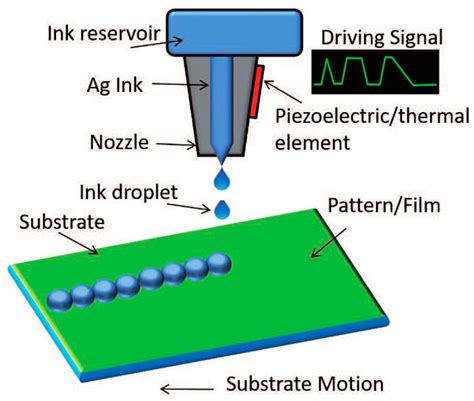

Frequently Asked Questions
What is the most common label application method?
+The most common label application method is machine application, which is widely used in high-volume labeling operations.
What is the best label application method for small-scale labeling operations?
+Hand application or thermal transfer labeling are ideal for small-scale labeling operations, as they offer a balance between precision and efficiency.
What is the difference between thermal transfer labeling and inkjet labeling?
+Thermal transfer labeling uses heat to transfer images and text onto labels, while inkjet labeling uses a printer to apply ink-based labels onto products or packages.